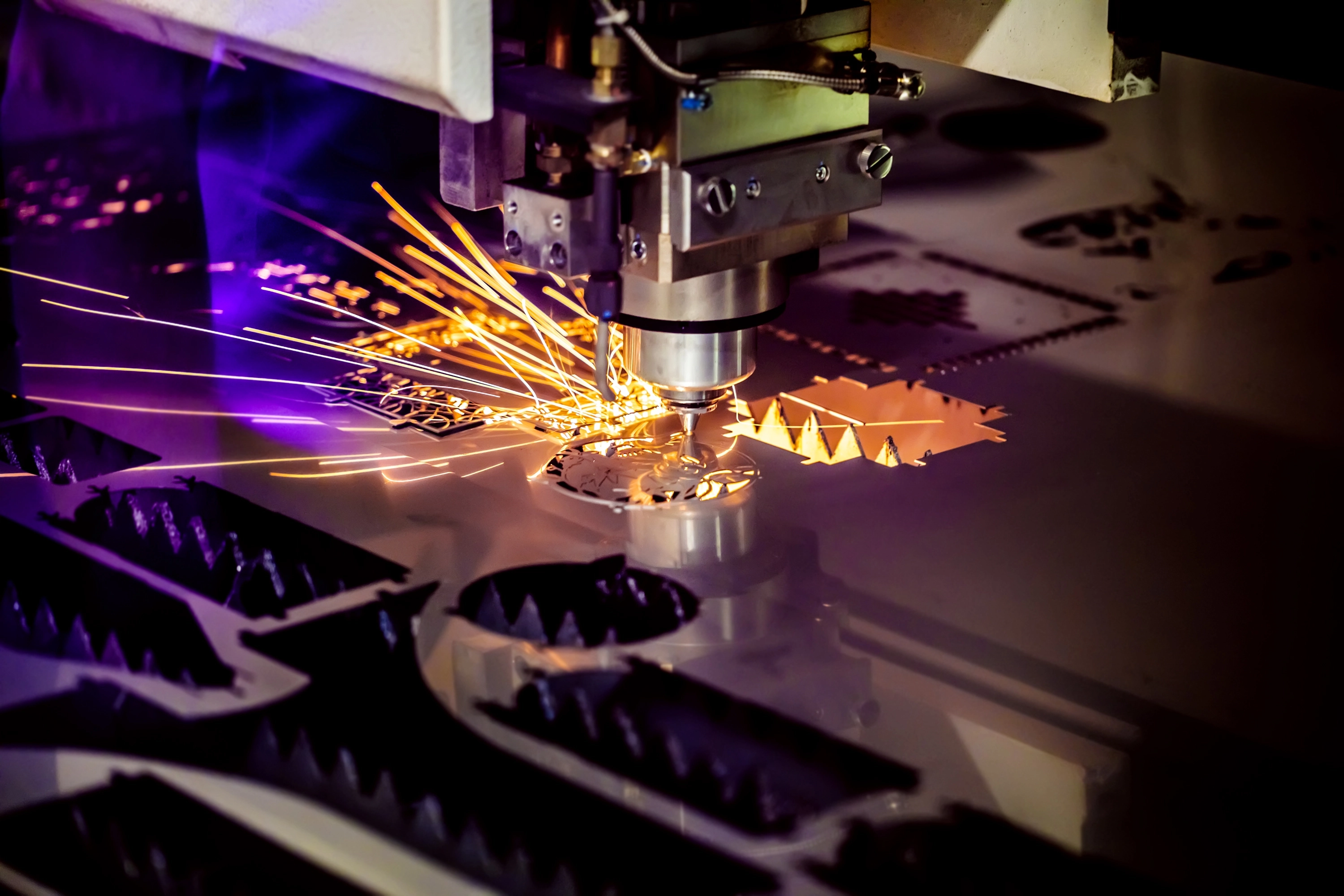
Laser Cutting
Efficient Programming for Flat Laser Cutting Machines with Almacam Cut Software
Throughout its history, Alma has been at the forefront of supporting the evolution of laser cutting technology. With advancements in increasingly powerful and versatile machines, laser cutting has become a cornerstone in the sheet metal sector. Today, over half of Alma's global customer base boasts ownership of at least one laser cutting machine, highlighting the widespread adoption and importance of this innovative technology
The Technological Process
Laser cutting stands out as a thermal machining and cutting technique, harnessing the concentrated energy of a potent laser beam onto minute surface areas (ranging from 0.1 to 0.5 mm). This method boasts rapid implementation and execution, significantly truncating production cycles while maintaining reliability and adaptability.
Primarily utilized for thin metal sheets, laser cutting swiftly fabricates simple or intricate shapes from diverse materials with thicknesses up to 25 mm, ensuring exceptional precision. The high-precision laser beam and absence of material surface contact prevent deformation or loss, rendering laser cutting exceptionally efficient. Perfect for prototyping and suitable for medium to large series manufacturing, it facilitates streamlined production processes.
The three primary types of laser cutting processes include CO2, Yag, and fiber. CO2 lasers excel in handling large thicknesses, whereas fiber laser cutting enhances performance and cost-efficiency for small to medium thicknesses. Presently, fiber laser cutting garners significant investment in the realm of 2D laser cutting machines, signifying its growing prominence and adoption."
Almacam Cut excels in laser cutting machine programming with top nesting efficiency, universal laser cutting support, precise parameter management, and automated workflows, ensuring unparalleled productivity
Substantial material savings
- Decreased loss rate attributed to high-performance automatic nesting with multiple strategy options
- Optimized nesting for standard cutting
- Efficient management of multiple nesting layouts for large-scale production
Reduced programming durations
- Automatic assignment of cutting characteristics, such as lead-ins/outs and reconfiguration loops
- Seamless automatic nesting functions with minimal user intervention
- Option for full automatic operation mode
Streamlined time cycles
- Efficient computation of tool paths for optimized performance
- Automatic computation of tool paths utilizing various strategies for common cuts, including rectangular grid or precutting neighboring parts
- Automatic collision detection and generation of swift trajectories in 'head-up' or 'head-down' modes
- Accelerated cutting of hole matrices facilitated by the quick grid function, which includes lead-in/out positioning, profile splits, and strip sequencing to enhance grid cutting efficiency by minimizing laser power interruptions
Proficient mastery of both technological processes and intricate machinery
- Automatic management of parameters based on cutting conditions (gas, lens) and profile sizes
- Versatile handling of various laser drilling modes
- Intelligent management for cutting sheets covered with plastic film, mitigating burning or vaporization issues
- Comprehensive support for all laser cutting machines and associated processes, including cutting conditions, drilling, engraving, tack welding, and micro-welds
- Extensive compatibility with a diverse array of machine-specific features, such as managing work areas for machine repositioning
- Capability to control programmable beveling heads while automatically preparing programs, including pass sequence and offsets calculation, reconfiguration loop or lead-in/out generation, overall profile adjustment to accommodate part bulk in nesting, and allocation of cutting conditions based on angle
- Seamless interaction with combined machines, such as those integrating laser and punching functionalities
Seamless integration with sheet metal CAD/CAM systems.
- 3D import capability for folded sheet metal parts
- Integration with the Sheet Metal Unfold module for importing and geometrically modifying or machining folded parts.
- Integration with Alma CAM Bend module for adjusting dimensions of unfolded parts based on tooling specifications
Enhancing the Quality of Manufactured Parts
- Automated parameter adjustment based on cutting conditions, such as gas type, lens specifications, and profile size
- Automatic generation of lead-ins/outs, considering material, thickness, and correction of erroneous lead-ins/outs.
- Utilization of diverse reconfiguration loops to optimize cutting outcomes, especially on corners
- Strategic heat distribution across the sheet through tailored cutting sequences
- Efficient management of skeleton cutting, offering customizable parameter configurations to clear obstacles or flatten the sheet prior to cutting
- Capability to re-initiate a program for cutting individual parts as needed
Safety-Oriented Programming
- Multiple collision prevention strategies: lifting the head, parabolic trajectory, cut part bypass, or employing specific sequences to minimize risk when passing over cut parts
- Height control feature enabling cutting near the sheet edge.
- Capability to secure small parts with micro-junctions to prevent them from falling under the table
Enhanced Workshop Handling
- Efficient management of skeleton cutting with customizable parameter settings to simplify cut-off removal
- Automated evacuation of inner profiles by dividing them into smaller pieces, eliminating the need for manual evacuation or trapdoor usage
- Systematic management for part evacuation (trapdoor, lift) and sorting (palletization)
- Hierarchical nesting with priority groups for easy sorting of parts during evacuation